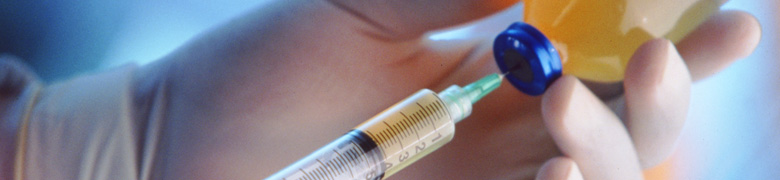
The scale and speed of the global vaccine research and development effort in response to COVID-19 is unprecedented. Researchers are exploring many different types of platforms for the development of COVID-19 vaccines, from the more traditional live attenuated virus and inactivated virus approaches, to recombinant protein antigen candidates, to newer approaches such as nucleic acid vaccines, like mRNA, which are showing promise in early stage phase 1 and 2 clinical trials.
Novel manufacturing technologies like micro-modular platforms for manufacturing of vaccines with increased speed are also being fast-tracked to address the problem of producing hundreds of millions of doses of the vaccine(s) at affordable prices for the global population.
No matter which vaccines ultimately are approved and which approach(es) is found to be the most effective, several manufacturing challenges must be overcome to ensure these vaccines are widely available in a timely fashion.
There are many areas in vaccine development and manufacturing where existing public quality standards, such as the ones in the United States Pharmacopeia–National Formulary (USP–NF) Online, can help.
The USP–NF is among the most comprehensive sources for medicine quality standards in the world. These standards include analytical methods, specifications, procedures, assays and other guidelines to assess product safety and quality. Companies and research groups can use these standards to get therapeutics to market more efficiently. USP’s documentary and physical reference standards can save time and resources that would have to be devoted toward development of in-house processes. Furthermore, since USP standards are recognized by many regulatory bodies around the world, they can help achieve more regulatory predictability.
USP public quality standards are developed through a collaborative process in which USP staff support Expert Committees made up of volunteers from industry, healthcare practitioners, academia and regulators, a structure that has been in place throughout USP’s 200-year history.
When questions arise, such as with nucleic acid-based vaccines, USP is in a unique position to foster collaboration with stakeholders and quickly work to help resolve these questions. Our scientific staff and volunteer bodies are ready to offer solutions to address development and manufacturing challenges, even and especially when some of these challenges cannot be addressed by our existing standards.
For example, USP can turn to the expertise of our staff and volunteers to convene an Advisory Expert Panel to offer solutions to specific challenges regarding novel vaccine platforms. In addition, USP is actively exploring new standards, like RNA standards, which would be useful for development of some vaccine platforms. Virus-like particles are also an area of active research toward novel standards. Importantly, USP has a lot of experience developing and validating assays, and if new assays are needed for a vaccine platform, USP may be able to provide advice regarding a particular assay format.

Public Quality Standards That Support Large-Scale Manufacturing of Vaccines
The overall goal of a commercial-scale vaccine manufacturing program is to produce millions of doses that are consistent in quality and safety with every production run. To accomplish this, the manufacturer must ensure vaccine production occurs in cGMP-compliant environments consisting of processes, physical facilities, procedures, personnel, documentation, training and quality systems to guarantee batch-to-batch consistency, with little room for variation.
However, as with all biological manufacturing processes, manufacturers should also expect that some variation can occur during the vaccine’s manufacturing process, and therefore, the process must be continually monitored to identify unanticipated changes in production that may influence vaccine quality and safety. Furthermore, over the life cycle of a vaccine, process improvements will also likely be implemented to increase efficiency and reduce cost, but manufacturers need to consider how these changes affect the critical quality attributes for the vaccine to ensure its continued safety and potency.
Depending on the type of vaccine that is developed, several components need to “pass” quality requirements to allow for large-scale production. Raw materials, growth media, cell substrates, production cell lines and other materials used in manufacturing vaccines need to be qualified for their intended use. Batch numbers must be clearly assigned, and the relationship between cell harvests and final batches of vaccine doses must be clearly differentiated.
Though many of these considerations are well known in the U.S. and other developed countries, and subject to regulatory requirements, many smaller vaccine developers and manufacturers can benefit from USP standards to facilitate the approval of their products by their own regulatory authorities.
Qualification and Control of Vaccine Components
Approved vaccines may contain numerous components that need a high level of quality control. These include the vaccine antigens themselves, adjuvants, antimicrobial preservatives and stabilizers, among other components. Process-related impurities from the manufacturing process must also be monitored and controlled to fall within prespecified limits.
Purification of biological products, like vaccines, is an area where public standards can be used to establish control of the manufacturing process. Numerous USP general chapters address various aspects of purification and analysis of biologic products, including detection of potentially harmful impurities.
General chapters found in the USP that may prove useful when manufacturing vaccines in large scale include the following:
- <1> Injections and Implanted Drug Products—Product Quality Tests
- <71> Sterility Tests
- <85> Bacterial Endotoxins Test
- <151> Pyrogen Test
- <1044> Cryopreservation of Cells
- <1048> Quality of Biotechnological Products: Analysis of the Expression Construct in Cells Used for Production of r-DNA Derived Protein Products
- <1049> Quality of Biotechnological Products—Stability Testing of Biotechnological/Biological Products
- <1050> Viral Safety Evaluation of Biotechnology Products Derived From Cell Lines of Human or Animal Origin
- <1074> Excipient Biological Safety Evaluation Guidelines
- <1116> Microbiological Control and Monitoring of Aseptic Processing Environments
- <1132> Residual Host Cell Protein Measurement in Biopharmaceuticals
- <1229.4> Sterilizing Filtration of Liquids
Guidance on how to control the quantity and size of any residual host cell DNA and host cell proteins can also be determined using General Chapters <1130> Nucleic Acid-Based Techniques—Approaches for Detecting Trace Nucleic Acids (Residual DNA Testing) and <1132> Residual Host Cell Protein Measurement in Biopharmaceuticals.
Some general chapters are also directly applicable to vaccines, whether still in development, ready to be tested in clinical studies, or approved and manufactured for commercial use. These chapters include the following:
- <1234> Vaccines for Human Use—Polysaccharide and Glycoconjugate Vaccines
- <1235> Vaccines for Human Use—General Considerations
- <1238> Vaccines for Human Use—Bacterial Vaccines
Biological assays (also called bioassays) are an integral part of the quality assessment required for the manufacturing and release of many biological and some non-biological drug products. In the USP are numerous general chapters regarding bioassays, including the following:
- <111> Design and Analysis of Biological Assays
- <1032> Design and Development of Biological Assays
- <1033> Biological Assay Validation
- <1034> Analysis of Biological Assays
- <1103> Immunological Test Methods-ELISA
The USP also has a series of general information chapters that provide techniques that support procedures for the detection and analysis of nucleic acids. Nucleic acid-based assays are used in a variety of settings, the most common of which include the detection of infectious agents (viruses, bacteria, etc.) and residual cellular DNA:
- <1125> Nucleic Acid-Based Techniques—General
- <1126> Nucleic Acid-Based Techniques—Extraction, Detection, and Sequencing
- <1127> Nucleic Acid-Based Techniques—Amplification
Packaging and Distribution
Making a pharmaceutical product is just part of the overall challenge. Preparing the vaccine for global distribution requires careful preparation and planning. Doses of a vaccine must be filled into single-use or multiuse vials and many vaccines need to be kept cold until ready for administration (the cold chain). Again, regardless of the type(s) of vaccine(s) that ultimately gets approved, packaging and distribution will play a crucial role in successful mass vaccination.
Each manufacturer will need to source ingredients and components to distribute its final vaccine product that are highly specialized and that come from only a handful of suppliers. Production of glassware, stoppers, syringes and other materials will have to be scaled up by other industries, and those will have to meet quality requirements for these types of components. The cold chain will also have to be maintained (if required) to ensure worldwide accessibility to the vaccine.
USP has a host of standards focused on packaging and distribution that could be invaluable to vaccine manufacturers. These and other standards and guidelines are available free of charge, but more importantly, USP has the ability to convene experts to discuss and help resolve unpredictable issues that our current standards do not address. Currently available general chapters on packaging and distribution include the following:
- <1027> Package Integrity Evaluation—Sterile Products
- <1031> The Biocompatibility of Materials Used in Drug Containers, Medical Devices, and Implants
- <1079> Good Storage and Distribution Practices for Drug Products
- <1178> Good Packaging Practices
- <1663> Assessment of Extractables Associated With Pharmaceutical Packaging/Delivery Systems
- <1664> Assessment of Drug Product Leachables Associated With Pharmaceutical Packaging/Delivery Systems
- <1787> Measurement of Subvisible Particulate Matter in Therapeutic Protein Injections
- <1788> Methods for the Determination of Particulate Matter in Injections and Ophthalmic Solutions
- <1790> Visual Inspection of Injections
For a description of the standards mentioned in this sections and other information about manufacturing and distribution of quality vaccines, visit our Trust Accelerated hub.
Supporting COVID-19 Vaccines Manufacture With Free Access to the USP–NF Online
USP understands the enormous challenges scientists, developers and manufacturers face as they race to develop and ultimately distribute quality vaccines and treatments for COVID-19 around the world. To help expedite this work, we are offering six months free access to the USP–NF Online.
Learn more and submit an online request today to receive expedited access to the USP–NF Online.
Additionally, USP’s scientific experts can provide technical support on the following topics:
- Regulatory expectations and analytical requirements for system suitability, control for contamination and assay validation
- Qualifying raw materials to be used in manufacturing
- Safety and qualification of biologically derived/complex materials
- Supplier risk management, including setting expectations based on raw material attributes and process impact.
Contact USPBiologics@usp.org with questions or for more information.